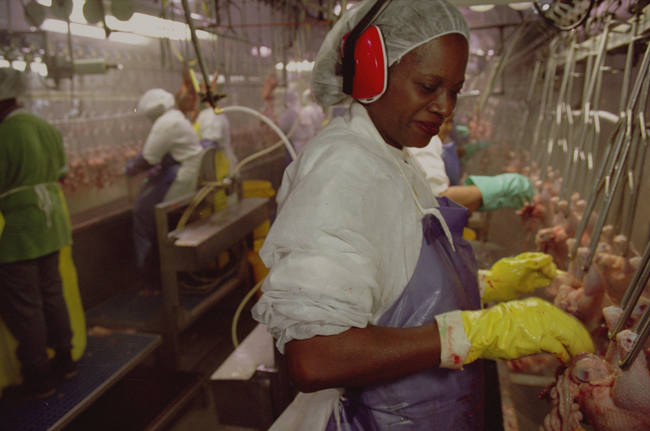
Earlier this year, the UFCW and Tyson commemorated 30 years of working together for safer workplaces by expanding our collaborative efforts to make workplace safety improvements at the company’s food processing plants. The innovative program broke ground by training and involving hourly production workers in identifying safety and ergonomics problems at their worksites. While the primary focus had been Tyson Foods’ beef and pork operations, it is now being expanded to the company’s poultry business.
Ergonomics, which is the science of designing the workplace to fit the worker, had not been extensively used in the meat industry until the UFCW and Tyson reached an agreement after an historic OSHA citation and settlement in late November 1988 followed up with the joint Tyson-UFCW program to develop a comprehensive ergonomics research program.
The program got underway in early 1989, with the company’s Dakota City, Nebraska, beef complex serving as the pilot plant, and production workers represented by UFCW Local 222, were actively involved. Due to the success of the pilot, the program was quickly expanded to all of the company’s beef and pork plants.
Some of the key elements of the program include ongoing ergonomics training for production workers; the involvement of hourly workers as ‘ergonomic monitors;’ worksite analysis and the redesign of work stations and equipment; and a medical management program focused on early detection and treatment of workplace injuries and illnesses.
Using ergonomic principles, properly designed jobs, tasks, equipment and tools as well as good job organization can help to fit the job to the workers.
Ergonomics includes:
- Designing equipment that is easy to use
- Investing new equipment that will take the strain out of the job
- Organizing work in different ways
- Changing how tasks are done
“We’re proud of the progress we’ve made through our collaboration with the UFCW, and especially the active involvement of frontline team members,” said Steve Stouffer, president of Tyson Fresh Meats. “We know that all of us must remain diligent if we’re to achieve additional improvements.”
“We value the progress we’ve made at Tyson and are looking forward to expanding our partnership to create safer workplaces for all of their hard-working men and women,” said Mark Lauritsen, director of the UFCW’s Food Processing, Packing and Manufacturing Division. “Working together with Tyson has meant empowering workers and their union to make a better, safer workplace.”
Early warning signs of repetitive stress may include: hand pain or numbness; stiff fingers; swelling in the hand, wrist, or forearm; and back or shoulder pain.
What are CTDs, RSIs, and MSDs?
Source: National Institute for Occupational Safety and Health (NIOSH) and United Auto Workers, Ergonomics Awareness Manuel.
Cumulative trauma disorders (CTDs) are disorders of the muscles, tendons, or nerves. CTDs are caused by repeated stress or exposure to forceful exertions, repetitive motions, awkward body postures, nerve compression and vibration. CTDs typically affect the arms, shoulders, hands or wrists.
Repetitive strain injuries (RSIs) is a general term like (CTD) used to describe a range of symptoms associated with repetitive motion work.
Musculoskeletal disorders (MSDs) are disorders of the muscles, nerves, tendons, ligaments, joints, cartilage, or spinal disks. Examples of jobs likely to cause MSDs are those requiring:
- Forceful or prolonged exertions of the hands
- Heavy lifting
- Pushing, pulling g or carrying of heavy objects
- Prolonged awkward postures
CTDs, RSIs, and MSDs are often used to mean the same thing.
The Three Stages of MSD Symptoms
MSD symptoms can range from mild aches to disabling pain. Symptoms often appear gradually and become more sever over time. Generally symptoms progress through three stages.
Stage 1
Symptoms may appear during periods of activity and may disappear during periods of rest. Symptoms are relatively mild. Early symptoms of MSDs often are mistaken for muscle fatigue.
Stage 2
Symptoms are most persistent. They do not disappear completely during periods of rest. Increasingly severe symptoms may interfere with performance of usual work activities.
Stage 3
Symptoms are constant. Sleep is often disturbed. Sever pain, limited mobility, loss of sensation or muscle weakness makes it impossible to perform most job tasks.
Symptoms of MSDs
- Soreness
- Burning sensation
- Numbness
- Weakness
- Tenderness
- Swelling
- Tingling
- Aching
- Stiffness
- Skin Discoloration (blanched or white) – skin discoloration of the fingers is an indication of Hand-Arm Vibrations Syndrome (HAVS) and it is the result of long-term exposure to vibration.
MSD Risk Factors
Many jobs that poultry workers do are associated with ergonomic risk fact that include:
- Repetition – performing the same motion or series of motions continually of frequently.
- Forceful exertion – the amount of physical effort to perform a demanding task or to maintain control of equipment or tools
- Awkward and static postures – assuming positions that place stress on the body, such as reaching above shoulder height, kneeling, squatting, leaning over a worktable, twisting, the torso while lifting, maintaining a sustained posture for a long period of time, as well as holding or using tools in a non-neutral or fixed position.
- Vibration – using vibrating hand-held power tools can increase the stress on the hands and arms.
- Cold temperatures